Production and Quality Control of Rail Sleeper
Steel mould
Steel mould shall be characteristics of adequate strength, rigidity and stability. It shall be able to ensure the shape, size and exact location of embedded parts of rail sleeper. It shall be done the routine and periodic inspection whose results shall be recorded in the checklist. The unqualified steel mould must not be put into use.
Feeding of sand, stone and cement
- A. According to the situations of storage silos for sand and stone, the feeding work shall be arranged. There must have time intervals for sand and stone feedings to ensure that sand and stone are not mixed.
- B. wood pieces, brick blocks, scrapping iron & steel blocks and other debris shall not be mixed into material silo. It is found that there are problems about sand and stone quality, the feeding work shall be stopped immediately and then technical staff shall be notified to deal with them.
- C. As cement silo is being fed, the material level shall be always observed to avoid overload. After the end of cement feeding, the dustproof bag shall be done the rapping work and checked whether it is good or not.
Mould cleaning and releasing agent spraying
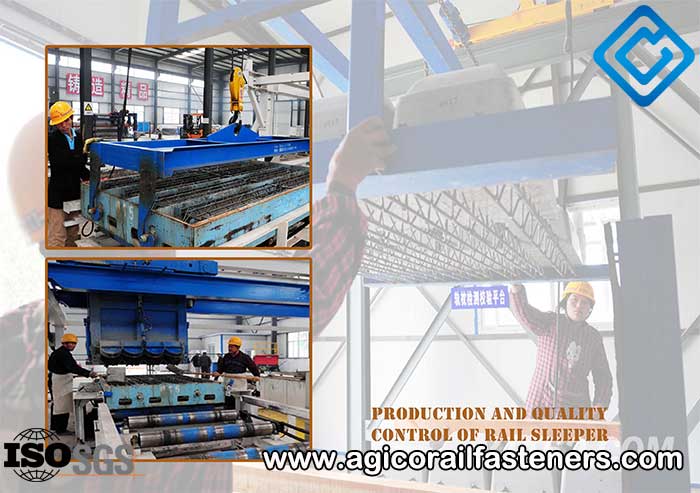
After the demoulding work, steel mould shall be conveyed through the roller table to the mould cleaning table and releasing agent spraying table. Here residual concrete and stickum in the mould shall be cleaned up and steel mould shall be also inspected. For loosened, floating or unqualified signs or number plates that are incomplete, they shall be lifted out to have a repair and maintenance. When steel mould is in line with the requirements, it will go into the next process. The releasing agent spraying must be even and uniform with the appropriate amount. The excessive dust shall be cleaned up with a rag. It is prohibited to use a metal hammer to hit the embedded parts of the mould. The hit maybe brings about the risk of inside deformation.A. Main and auxiliary equipments of cleaning steel mould
-
A. Main and auxiliary equipments of cleaning steel mould
Rags, pails, spatulas, high-pressure air guns, hammer chisels, grinders, releasing agent, graphite sprays, pipe pliers, tables for instruments. -
B. Releasing agent spraying
Spray releasing agent on the entire inside surface of the mould with a sprayer. The nozzle shall be aligned above the mould. Adjust the releasing agent into mist mode rather than nonlinear drop mode. The spraying surface must be kept dry.
Casing installation
After the mould is sprayed with the releasing agent, it will enter installation table of the embedded casing through roller table. Install the casings to the vacuum rubber rods and move it left and right to secure right positions so that the casings are not damaged in the fixed positions. If necessary, clean them; if damaged, replace new ones. The holders must be absolutely clean. Before the installation, and they shall be treated with graphite spray. After the installation, the bent steel bars and steel mesh are not fixed on rail grooves. When everything meets the requirements, the mould will enter the next process. We must make the must-be casting visual inspection. Visual inspection: Burr /contamination. Pick out unqualified castings, hold them in the fixed positions, verify whether the additional steel bars are contaminated or not, for example, releasing agent contamination.
Steel truss into the mold
- A. Put steel mesh with distance clamp at each supporting rail groove in the mould
- B. When installing steel truss, it must be inserted into the necking of the mould
- C. Make sure that the truss reinforcements are on the fixing hook
- D. Make sure that the truss reinforcements are placed against the wedges
-
E. Use tension device to fix truss reinforcements
After the truss reinforcements are fixed on the mould, install the retaining clamps with the flat side facing the inside of the mould shell and the curved side facing the end of the mould. After the installation, the accessories shall be checked in time. - F. Precautions
After the installations of casings, bent steel bars and steel mesh, the mould will go into the installation platform of truss reinforcements. The installation must be in accordance with design drawings. The truss reinforcements cannot contact with the casings. The thickness of concrete protective layer shall be ensured to avoid the truss reinforcements being restrained. The deformed truss reinforcements shall not be used. The spring fixing device can make truss reinforcements not be constrained during fixing truss reinforcements. The spring must achieve a certain stiffness to achieve the effect of securing the truss reinforcement without restraints. The mould will moves to the next process by a car and roller table.
Concrete pouring and vibrating
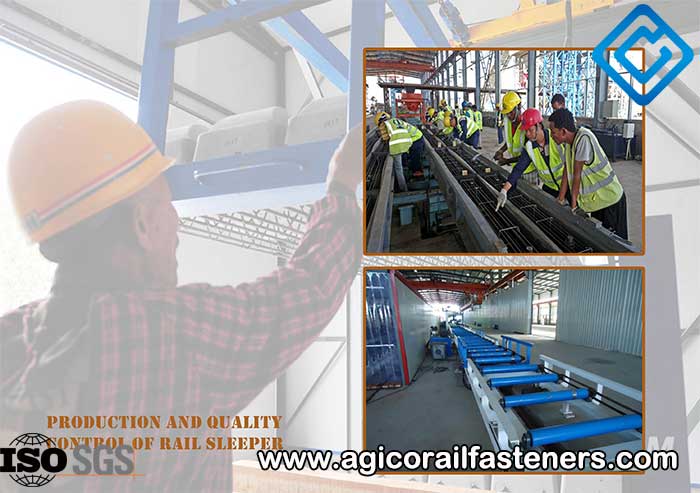
After the truss reinforcements, upper girder, bent steel bars and casings are installed in the mould and before the pouring concrete, the positions and the spacing of the steel bars and the embedded parts shall be confirmed. The mould shall be moved in traverse direction to concrete vibrating table by roller table and the trolley. And then the pneumatic lifting rollers on the vibrating table are down. The mould falls down on concrete vibrating table. The concrete placing car moves to the vibrating table with the mould. The first layer of concrete will be placed and vibrated, and then the second layer of concrete will be done. As the concrete meets the requirements, the vibration will be on for about 2 minutes. As the vibration stops, the pneumatic lifting rollers will be lifted, and then the mould will move to the next table. The concrete pouring temperature shall be strictly controlled, and the mould temperature of concrete mixture shall be controlled in the range of 5℃-30℃. The temperature of fresh concrete shall be in the range of 15℃-25℃. When the average temperature in day and night is below 5℃ or the lowest temperature below -3℃, It is key to take insulation measures for aggregate, cement and mixing water, etc. according to the winter construction requirements. It shall make various parts of mould be poured moderate and uniform by use of the concrete placing machine as far as possible. Excessively dry or too wet mixture shall not be put into use. The material shall be divided into two layers at least. The debris shall be removed in time. There shall be no concrete on both ends of the mould. Compaction shall be carried out automatically. Metal cover can be used to store concrete. During the vibration, a shovel can be used to add or remove necessary or unnecessary concrete. We should pay more attention to check the compactness of concrete during vibration and observe whether the sleeper thickness is suitable.
Disassembly of accessory parts and cleaning of slag and edge
Pull the retaining clamps out and put into the box to clean. Use the scraper to deal with the spilled concrete.
AGICO Group owns rich experience and advanced equipments in railway accessory. We can help you solve the above problems!
As a professional railway enterprise, AGICO Group is major in railway products with good quality such as steel rail, rail sleeper, rail fastening systems, rail fishplate, rail tie plate, rail bolt, railroad spikes, steel dog spike, etc. They are exported all over the world. Depending on more than ten years export experience, we can offer the most competitive price and highest quality for our customers all over the world because we are factory. In the other side, we can deal with the international business freely because we have an experience team in international department. They can offer the best service for our customers. We sincerely seek for reliable cooperators abroad to market the world. Welcome to contact with us!
We receive enquiries in English, Español (Spanish), Русский язык (Russian), Français (French) and العربية (Arabic). Our professional team will reply to you within one business day. Please feel free to contact us!